STEELING FOR SAFETY
“THE SMART OPERATORS HAVE FINALLY REALIZED THAT TO BE A GOOD NEIGHBOR, THEY CAN’T BUILD TIN CANS”
Mark Caskey,
Steel Nation President
BY MICHAEL BRADWELL
Energy editor
Mark Caskey’s experience in the Marcellus supply chain is similar to many other area businesses that found it took some time to gain a foothold with oil and gas exploration companies. When Caskey officially launched Steel Nation in 2008, the company was offering design and construction services that included mixed-use flex buildings for offices, warehouses and manufacturing, coal processing plants and natural gas compression stations.
But within a few years, Caskey found his business tilted toward structures that house natural gas compression stations. He also found that companies are more willing to build stations that contained more sound suppression and were better ventilated. Developing a niche four years ago, Caskey said, he was knocking on the doors of Range Resources and Mark West, but to little avail. “I couldn’t get anywhere, but then I bid a job for Atlas Energy.” That let to Steel Nation erecting nine building for the company’s single-engine compression stations.
Today, Steel Nation is a leading supplier of transmission, storage and midstream compressor stations, building many structures for compressor stations operated by MarkWest, Chesapeake and Williams. According to trade magazine Metal Construction News, Steel Nation was ranked 14th in the country in 2011 among metal construction companies, with a total steel tonnage of 2,224 tons, up nearly 20 percent from 1,855 tons used in 2010. In 2011, it built 389,526 square-feet of facilities. According to Caskey, the company, which is on track to produce more than $20 million in sales this year, is designing and building turnkey compressor stations that are safer, cooler and more quiet than units constructed in the earlier days of the Marcellus Shale exploration and build out. “These are the types of buildings I want to build,” Caskey said. “The smart operators have finally realized that to be a good neighbor, they can’t build tin cans,”
According to Caskey, the company’s major focus is designing, manufacturing and building the safest facilities in the energy sector. “There’s no one in the Marcellus doing what we’re
doing,” he said. The company is headquartered along Route 19 in South Strabane Township. While it has field offices in the Utica, Bakken, Eagle Ford and Barnett shale plays, the Marcellus remains its center of operations. The company has five fulltime employees, but uses subcontractors for building foundations and erecting the steel for its projects. “We have about 80 people in the field right now,” he said. The biggest challenge, he said, is designing a building to contain equipment that runs around the clock, produces extremely high temperatures and noise levels that exceed 100 decibels.
The buildings contain compressors that have heat gains of over 2 million British thermal units per hour. Caskey said his company designs ventilation systems to ensure that buildings stay cool at all times, using a proprietary system that will always provide at least a dozen air changes per hour, but averaging as much as 22 to 32 air changes in an hour. While compressor stations are unmanned, the buildings have to be designed to be explosion-proof. “There are technicians who come and go and do the readings,” he said. With 225 compressors under roof and counting, Steel Nation has never had a compressor shut down due to high temperatures, he said. He noted that in addition to the excess heat posing a combustion hazard, the barometric pressure and humidity in the air creates condensation that also transmits sound. So in addition to properly ventilating its buildings, Steel Nation also uses a number of sound mitigation techniques, based on local codes which include acoustic panels, mineral wool, batt insulation and perforated barriers to control sound and vibration, both produced from within the buildings and from exterior sound sources, he said.
While Steel Nation has built coal processing prep and power generation plants, furnishing and erecting coal warehouses, maintenance shops, bath houses and coal material handling buildings, Caskey said the company has seen its business emphasis shift to natural gas compression stations in the past couple of years. “There’s very few prep plants being built anymore,” he said.
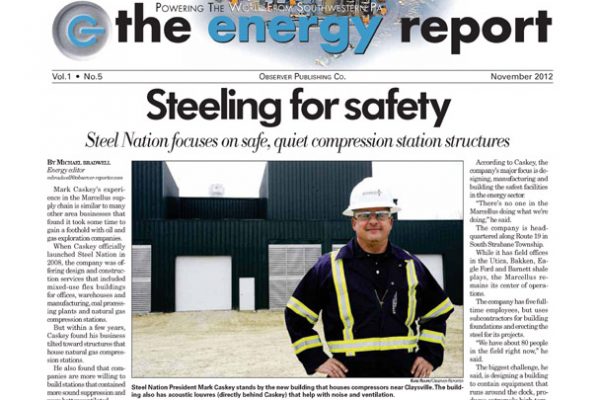